Atlanta run on May 5, offered visitors an overwhelming array of textile-related developments geared
primarily—but not entirely—to technical markets.
According to the organisers, the combined exhibitions enjoyed a 13% growth in square footage for 2016, with
a total of 519 exhibitors, and over 7000 visitors pre-registered. The shows were held in conjunction with the
JEC Americas Composites Show.
Unlike the Frankfurt show, however, exhibitors and visitors at the Atlanta edition were mostly focused on
doing business in the western hemisphere, where potential customers include 40% of the world’s consump
tion (by volume) of personal protective equipment (PPE), and a military budget of US$1.5bn
(according to OTEXA) for clothing and equipment which by law must be sourced domestically. US textile
mills are also finding opportunities in the market for nonwovens used in automotive and building insulations,
as well in bedding—components which are too bulky to ship long distances economically. In addition, several
of the major apparel brands are developing increasingly technical product and emphasizing manufacturing in
the West, utilizing automation and robotics to compete with less expensive offshore labour. “US brands and
retailers want production close to the market, and advanced technology is essential,” stated Dave Gardner,
managing director of the Sewn Products Equipment & Suppliers of America (SPESA), which co-produced
Texprocess N.A. New developments in PPE According to Mary-Lynn Langraf, senior international trade
specialist for the US Department of Commerce/OTEXA, the market for PPE is expanding beyond military,
first responders, and oil/gas/electrical workers to now include general industrial workwear and apparel for
recreation and sports. Comfort is a major issue, driving demand for light weight layers and better styling.
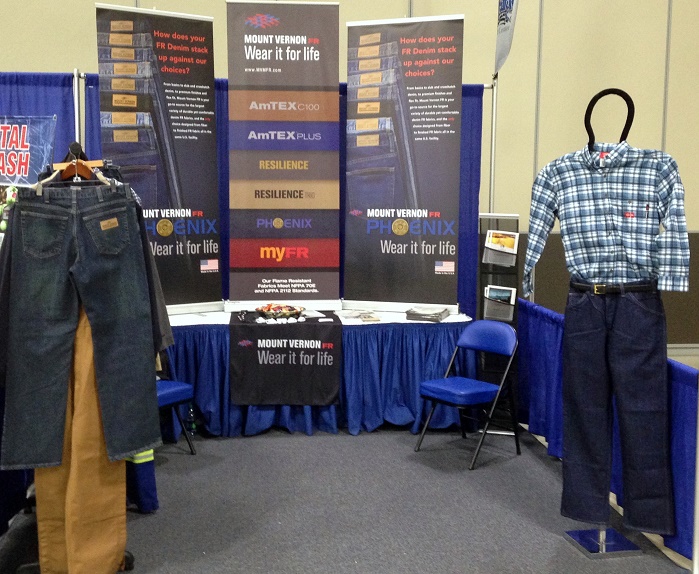
Fabric mills have responded with blends of natural and inherent FR fibres, and new technologies that wick
and breathe as well as protect. Mount Vernon Mills’ portfolio included AmTEX™ TC woven shirtings in blends
of cotton/TENCEL®; PHOENIX FR cotton denims in a wide range of weights; and inherently
FR RESILIENCE™ fabrics in blends of cotton/Nomex®. The company is vertical from yarn spinning through
weaving, dyeing, and finishing.
Safety Components’ patented Filament Twill Technology™ enabled lighter weight fabrics with improved
protection.
The twill weave, combining filament Kevlar® with a spun Kevlar® blend yarn, is said to be more comfortable
and flexible than the traditional rip stop fabrics used in firefighters’ turnout gear. At SSM Industries, Pro-CFR®
flame resistant cotton fabrics featured Cotton Incorporated’s TransDRY™ moisture management technology,
and an anti-odour treatment. The latest development at the company, which knits, weaves, dyes, and finishes
its own products, is a line of soft, wickable, no melt/no drip filament knits called Pro-FilFR®. Glen Raven
Technical Fabrics (GRTF) has added Hi-Vis and Hi-Vis Anti-Stat modacrylic blends to its GlenGuard FR fabric
line. “In general, we are seeing an increased demand for the traceability and peace-of-mind afforded by
US-sourced FR materials,” commented Rich Lippert, marketing director at GRTF.
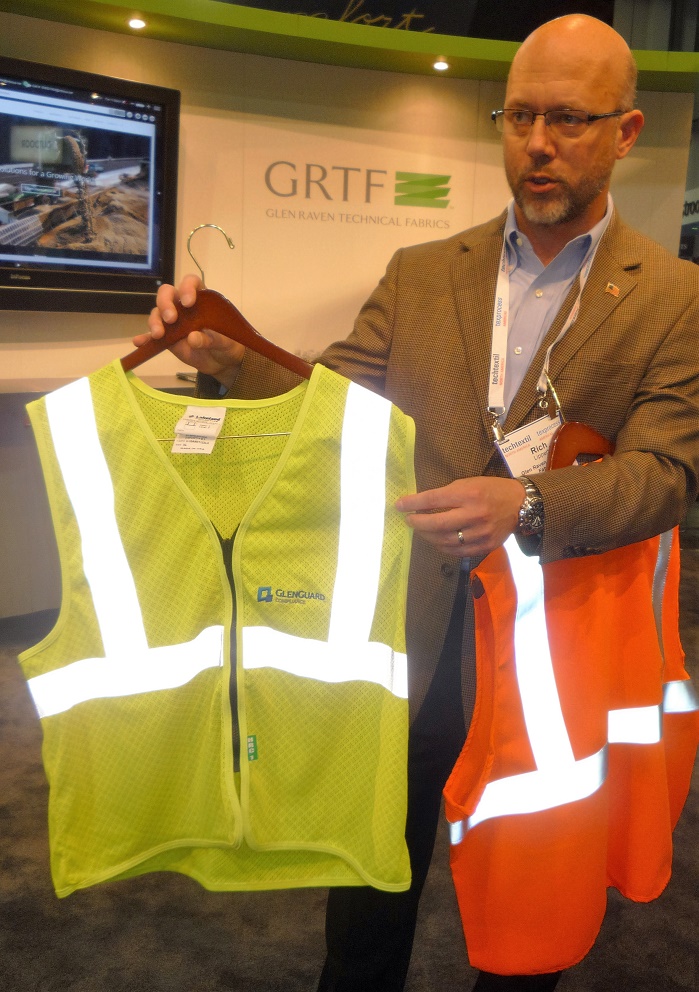
Knitters of traditional apparel fabrics, such as Coville, Minnesota Mills,
and Draper Knitting, were in agreement. “Our biggest market segment is fire service,” concurred Dave
Wedge, technical fabrics product manager for Draper. Yarn spinners such as National Spinning and
Pharr Yarns are increasingly focused on the PPE market. At Buhler Quality Yarns, known for their super
-soft Supima®, TENCEL®, and MicroModal® yarns, the push is on to develop “hybrid” yarns that will
“make pima cotton more technical,” confided VP of sales David Sasso.
Advancements in sustainable options The necessity to produce product in a more sustainable way
is driving innovation in all aspects of textile manufacturing, and there was a range of sustainable options
presented at the show for industrial textiles as well as in the apparel segment. Some 85% of the colourful
nonwoven insulations and bedding materials at Carolina Nonwovens, a division of National Spinning, were
created from recycled textile materials. Leigh Fibers, a 100-year-old textile recycler in South Carolina,
utilises everything from denim shoddy and spinning waste to Kevlar.
“Nonwovens is the biggest aspect of textiles in the US,” confirmed Uwe Deligne, Leigh senior account executive.
Poole Fibers’ EcoSure® BioBlast™, a biodegradable polyester fibre made from 100% recycled PET bottles
, targeted the nonwoven wipes industry. The soft, durable fibres were shown to biodegrade twelve times faster
in landfill conditions, over a year, compared with traditional petroleum-based fibres. The controversy
regarding durable water repellent (DWR) finishes containing perfluorinated chemicals (PFCs) is one of
the biggest challenges for manufacturers of performance and protective apparel. While the chemical suppliers
were mostly absent from the show, Massachusetts-based Bolger & O’Hearn took a stand to promote their
F3 fluorine-free finish, said to outperform many C6 DWR chemistries.
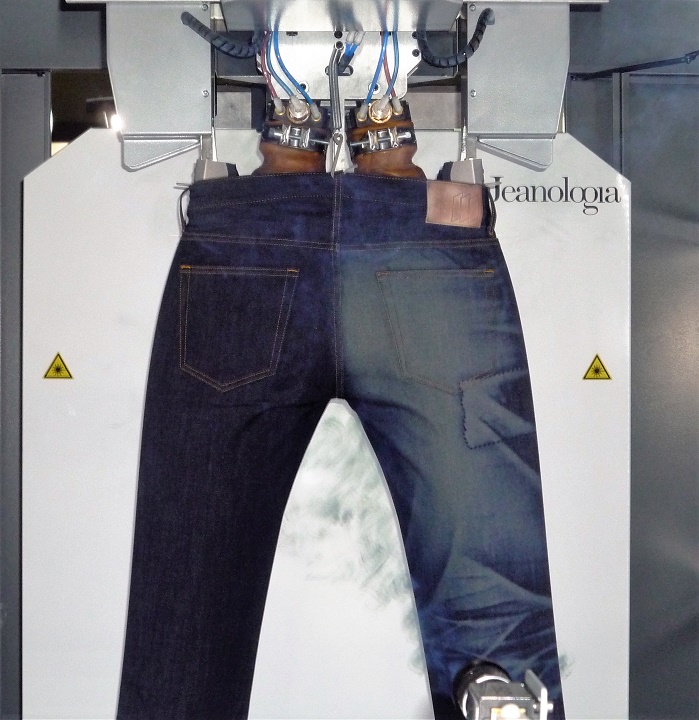
“Our fluorine-free product stands out for its performance past 20 washes,” explained sales manager Shawn
Honeycutt. “The adoption rate for fluorine-free DWR is not as high as it should be. The European brands are
much further along.” Another synthetic application under fire, polyurethane (PU), can now be replaced by
Covestro’s INSQIN®, a waterborne technology processed without solvent; eliminating harmful substances and
saving up to 95% of water normally used to wash the solvent out. The magic of the machine It’s hard to
surpass the dramatic impression made by the textile finishing machinery at the show. Jeanologia’s sustainable
technologies for finishing denim combined laser spray and nano bubbles to eliminate the use of damaging
chemicals and conserve water; and the onsite demonstration of its laser technique drew a crowd. While
ApJET’s plasma-based textile finishing machine was not on display, the company has “made a lot of progress,
” in areas such as FR and DWR chemistry, said director of sales, Martha Miller. Because the technology uses no
heat or water, which can degrade aramids or high-tenacity fibres, performance and PPE materials can potentially
be lighter in weight.
The company has also developed a unit to recycle the helium used to generate the plasma, which reacts with the
textile finishing chemistry to form a covalent bond.
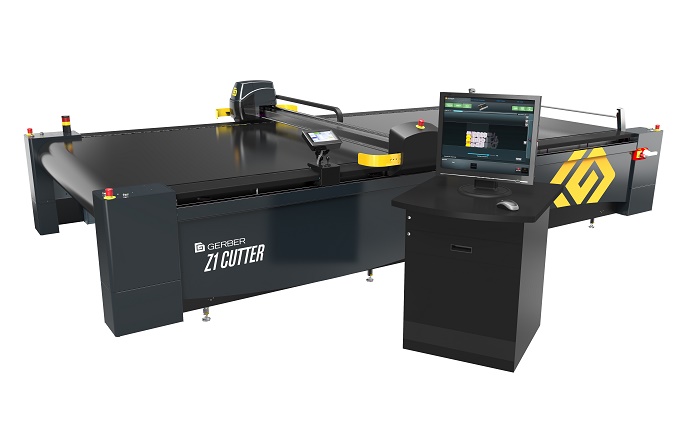
Digital ink-jet printing, used to print paper for sublimating prints on synthetic fabrics for the
athletics market, has been widely accepted as a more sustainable printing option. Gerber Technology’s Z1
cutting machine handles a whole roll of pre-printed individual garment pieces, eliminating wasted ink and
the need for pattern matching. The pre-printed, laser-cut pieces can go right to the sewer. From 2001 – 2013
, the US textile industry invested US$20.5bn in new plants, equipment, and recycling centres, according to
OTEXA. SPESA’s Gardner believes that the trend is continuing. “China and India are now seeing the advantages
of manufacturing in the US, ” he pointed out.
Debra Cobb presents her highly valued opinions on the very latest innovations in fibres, yarns,
knitted fabrics and garments.A veteran of the US textiles industry with international experience